Discover essential tips for a triumphant Windchill PLM implementation & rollout. Streamline your processes and achieve success with our expert guidance.
- Introduction
- Conduct a Comprehensive Needs Assessment
- Assemble a Cross-Functional Implementation Team
- Define Clear Implementation Roadmap and Timeline
- Thorough Training and Change Management
- Integration with Existing Systems
- Ensure Data Security and Compliance
- Continuous Monitoring and Optimization
- Conclusion
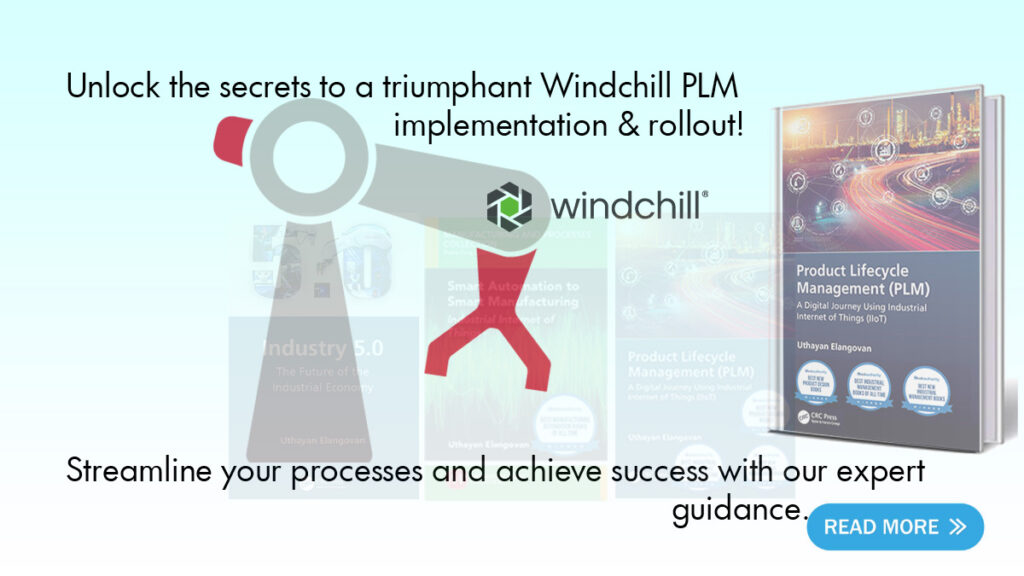
Introduction
Product Lifecycle Management (PLM) solutions have become integral for enterprises to streamline their product development processes, enhance collaboration, and drive innovation in today’s competitive manufacturing landscape. Among the top-tier PLM systems, Windchill stands tall as a reliable and feature-rich solution. However, successful Windchill implementation and rollout require careful planning, expert guidance, and a thorough understanding of the organization’s unique requirements. In this article, we will explore the tips and strategies for End-to-End Windchill PLM implementation and the efficient rollout of different functions in a manufacturing company.
Embark on a thrilling digital journey through the realms of Product Lifecycle Management (PLM) and Industrial Internet of Things (IIoT) with our acclaimed book, recognized as one of the “Best Industrial Management Books of All Times” and awarded the prestigious “2020 Taylor & Francis Award Winner for Outstanding Professional Book”!
Conduct a Comprehensive Needs Assessment
The first step towards a successful Windchill PLM implementation is to conduct a comprehensive needs assessment. This involves understanding the specific pain points, challenges, and business objectives of the manufacturing company. Engage stakeholders from various departments to gather insights and identify the key functionalities and features required from the PLM system. A detailed analysis will help in tailoring the Windchill implementation to align with the organization’s unique goals.
Assemble a Cross-Functional Implementation Team
Implementing Windchill PLM is not just an IT project; it requires collaboration from multiple departments across the organization. Assemble a cross-functional team with representatives from engineering, manufacturing, quality control, supply chain, and IT. This team should work closely with the PLM consultants to ensure that all the requirements are adequately addressed and that the solution meets the needs of each department.
Define Clear Implementation Roadmap and Timeline
A well-defined implementation roadmap is essential to keep the project on track and within the planned timeline. Break down the implementation process into manageable phases, each with specific milestones and objectives. By setting clear deadlines and monitoring progress regularly, potential roadblocks can be identified early, and necessary adjustments can be made to avoid delays.
Thorough Training and Change Management
Effective training and change management are critical for successful Windchill PLM rollout. Users across the organization must be adequately trained to use the new system efficiently. This includes not only technical training but also communicating the benefits of the PLM system to gain user buy-in. Addressing the concerns and resistance to change is vital to ensure a smooth transition to the new system.
Integration with Existing Systems
In most manufacturing companies, various legacy systems are already in place. To maximize the value of Windchill PLM, it is essential to integrate it seamlessly with these existing systems. Whether it is ERP, CAD software, or other enterprise applications, a well-integrated PLM system ensures data consistency and reduces redundancy, leading to improved efficiency.
Ensure Data Security and Compliance
Manufacturing enterprises handle sensitive data related to products, designs, and intellectual property. Implement robust security measures within Windchill PLM to safeguard this critical information from unauthorized access. Compliance with industry standards and regulations should also be a priority to avoid legal and financial repercussions.
Continuous Monitoring and Optimization
The implementation process doesn’t end with the initial rollout. Continuous monitoring of the PLM system’s performance and its impact on operations is crucial. Regularly gather feedback from users and stakeholders to identify areas for improvement and optimization. This iterative approach ensures that the Windchill PLM system evolves with the organization’s changing needs and technology advancements.
Conclusion
In conclusion, successful End-to-End Windchill PLM implementation and rollout in manufacturing companies require a strategic approach, comprehensive planning, and a commitment to embrace change. By conducting a thorough needs assessment, assembling a cross-functional team, defining a clear implementation roadmap, providing adequate training, integrating with existing systems, and prioritizing data security, enterprises can unleash the true potential of Windchill PLM.
If you’re a manufacturing enterprise looking to streamline your product development process, enhance collaboration, and boost innovation through Windchill PLM, NeelSMARTEC is your trusted partner. With years of expertise in PLM consulting, our team of experts will ensure a seamless and cost-effective Windchill PLM implementation tailored to your unique business needs. Contact us today to revolutionize your product development journey!
Disclaimer:
The information provided in this article is based on my experience with various clients in the context of End-to-End Windchill PLM implementation and rollout in manufacturing companies. While we have made every effort to ensure the accuracy and reliability of the content presented, it is essential to acknowledge that the specifics of Windchill PLM may vary depending on the individual company’s requirements and the version of the software being used.
Readers are encouraged to refer to the official documentation and resources provided by PTC (Parametric Technology Corporation) for Windchill PLM. PTC’s official documentation offers comprehensive and up-to-date information, including user guides, technical specifications, and best practices.