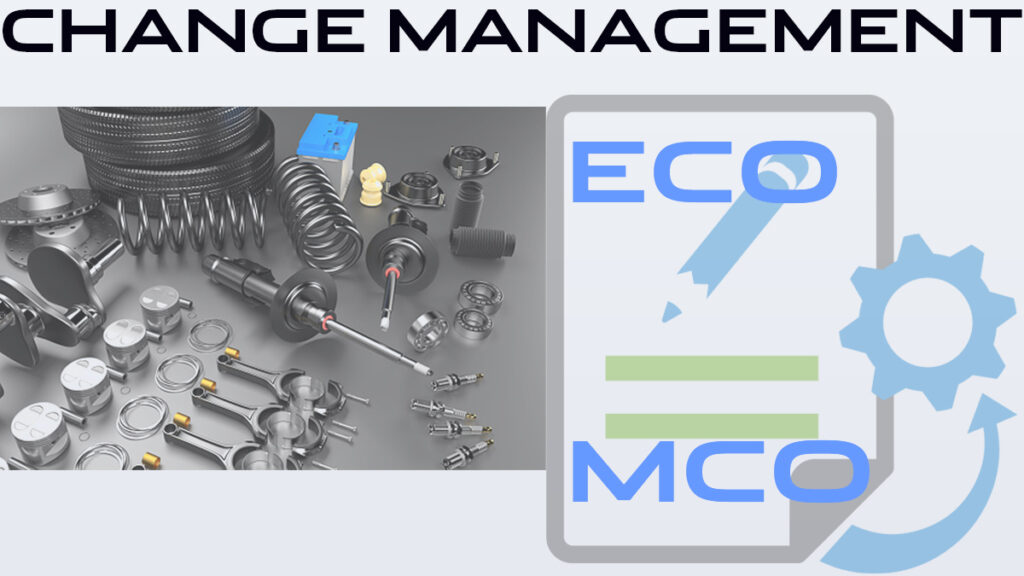
Change Management (CM) is an essential role in the product manufacturing industry that aids to keep order throughout the flurry of adjustments that happen in a life cycle of a product. Efficient CM involves product modifications redlining, version changes, effect analysis, adjustment orders, and workflow authorization procedures.
As technological breakthrough develops smart connected manufacturing processes, along with the ever-present need to produce in one of the most cost-effective means feasible, business must continually stay on their toes to identify and also exploit opportunities. Change management entails producing dynamic environment that understand the fact of modification, prepares effectively for it, and also capitalize at the correct time. A fascinating facet of change monitoring in a manufacturing industry is to take into consideration modifications that happen in design as well in production.
Changes are unavoidable throughout the product development process, as it’s essential that these modifications be taken care of effectively with a cross-functional group of professionals within the company to stay clear of squandering time, money and also resources on inaccurate parts. As product intricacy rises as well companies end up being more dependent on their supply chains, handling the CM and also interacting change status across several teams inside the enterprise and right into the supply chain is a raising challenge.
One of the classic example of implementing change process is while submitting part warranty to the customers via ECO as – International quality standards requirement for manufacturing keep on enhance for most of the industrial product manufacturers calling for their suppliers to utilize production part approval process (PPAP) while implementing change to the product or process. PPAP process should satisfy customer’s requirement of producing a new part or product, ECO needs to be implemented along with the documents authorizing the modification and requesting needs to be included in the PPAP package. Customer may request a PPAP at any time throughout the life of a product. For suppliers, this means preserving a quality system that develops, records every one of the requirements of a PPAP submission. It certifies that all areas of the design and production process have been assessed extensively to guarantee that high quality product will certainly be enabled to deliver to the consumer. Part submission warrant is a recap of the whole PPAP submission that specifies the declaration of material, associated drawing changes, part number, inspection results, and any deviations are covered by the PPAP submission.
As part / component / product complexity increases as well enterprises end up being extra based on their supply chains, taking care of the change management process as well as likewise communicating adjustment status throughout a number of groups inside the enterprise right into the supply chain is an elevating challenge. Change Management is a crucial function in the product manufacturing sector that helps to keep order throughout the flurry of modifications that occur in a product lifecycle. Reliable change process involves product adjustments redlining, variation adjustments, result analysis, adjustment orders, and workflow authorization procedures. Check out OpenBOM Change and PTC Windchill CM management process.
Implementing change process – Engineering Change Order (ECO) and Manufacturing Change Order (MCO) vary depends on the enterprise business process, consider the factor such as
From where it originated?
Why it is occurring?
How to fix the change?
Communicate the change to the NPD/NPI team members?
How the change process will affect the business process?
Task to be taken to implement the change?
CM consists of Problem report, Change Request, Change Notice, and Change Order. In short Engineering change orders (ECO) are utilized for adjustments in assemblies, documents, components and any other components related to product design and manufacturing. Change Control Board (CCB) is a board that makes decisions regarding whether proposed modifications to a change task must be implemented. Affected items are components, records, procedure plans, or various other revision-controlled things that will be affected by the modification. These are contributed to a job in the implementation plan of a modification notice. When an individual completes the designated job, generally these components are affected. Change could be anything from an adjustment in materials, design adjustment, manufacturing procedures that transform just how the kind, fit or function of the end product. Every modification should be appropriately evaluated by all the cross functional department along with quality assurance team to figure out the effect of the modification and carry out the modification through informing the customers. Change management within PLM gives the disciplined procedure to execute a change effectively with the least quantity of disruption.
An optimal manufacturing business (SMEs and OEMs) demands remarkable assimilation of ECO as well as MCO process that attends to the common concerns of manufacturers and inevitably provides various organization benefits. Main goal of the manufacturing enterprise is to function carefully to boost high quality, decrease scrap besides come to be extra effective in routine manufacturing which will certainly minimize our step-by-step costs of the end item.
Final Thoughts:
PLM automates and also improves ECO and MCO process, allowing task occur simultaneously. NPD/NPI team members can concurrently analyze change, able to analysis as well mark-up changes digitally. Too aids to track the history of the open ECO, MCO where it is pending, as well existing condition all are tape-recorded. Change notification intimate NPD/NPI team member that there’s a change implemented and encourages cross functional team members concerning exactly just how to apply the changes in engineering and manufacturing within the enterprise.