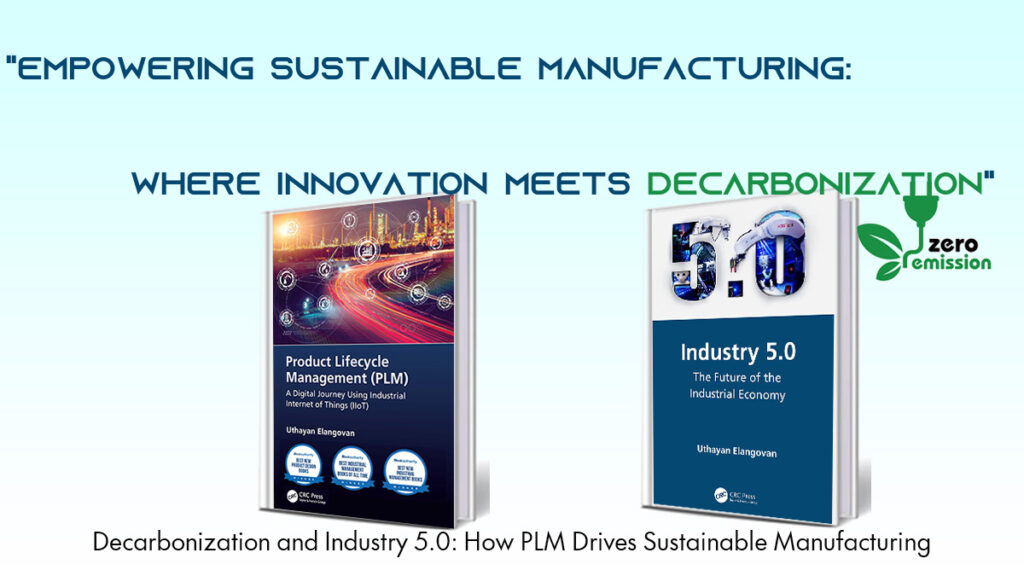
Introduction:
In today’s world, addressing climate change and reducing carbon emissions are critical priorities. The manufacturing sector, being a significant contributor to greenhouse gas emissions, is actively seeking sustainable solutions. This article explains, in simple terms, how Product Lifecycle Management (PLM) in the context of Industry 5.0 can play a pivotal role in decarbonizing manufacturing processes.
1. Understanding PLM:
Product Lifecycle Management is a strategic approach that manages the entire lifecycle of a product, from concept to disposal. It enables companies to effectively collaborate, streamline operations, and optimize resources throughout the product journey. By integrating various digital technologies and data, PLM facilitates efficient decision-making, enhances productivity, and reduces time-to-market.
2. Industry 5.0 and Sustainability:
Industry 5.0 represents the convergence of advanced manufacturing technologies, such as automation, robotics, and artificial intelligence, with human capabilities. It emphasizes the importance of human-machine collaboration and focuses on sustainable production. By combining digitalization and sustainability principles, Industry 5.0 aims to create environmentally friendly and socially responsible manufacturing systems.
Check out our Publications on
3. PLM’s Role in Decarbonization:
PLM serves as a powerful tool for decarbonization in the manufacturing sector. Here are a few ways in which PLM contributes to reducing carbon emissions:
a) Design Optimization: PLM enables designers to create sustainable products by incorporating eco-friendly materials, efficient manufacturing processes, and energy-saving designs. By analyzing environmental impacts at the design stage, manufacturers can minimize resource consumption and emissions.
Example: A PLM system suggests alternative materials for a product, helping engineers choose a more sustainable option that reduces carbon footprint without compromising quality.
b) Energy Efficiency: PLM can identify opportunities for energy optimization by analyzing production data, equipment performance, and energy usage patterns. It enables manufacturers to optimize production schedules, reduce idle times, and ensure energy-efficient operations.
Example: Using PLM analytics, a manufacturing plant identifies energy-intensive processes and implements measures to reduce energy consumption, resulting in significant carbon emission reductions.
c) Supply Chain Collaboration: PLM facilitates seamless collaboration among suppliers, manufacturers, and other stakeholders in the supply chain. By sharing data and coordinating efforts, companies can optimize transportation, minimize waste, and reduce emissions associated with the procurement and distribution of raw materials and finished goods.
Example: With PLM, a manufacturer collaborates with suppliers to optimize transportation routes, reducing delivery distances and associated carbon emissions.
d) Lifecycle Management: PLM provides visibility into the entire product lifecycle, including maintenance, repair, and end-of-life processes. This visibility helps optimize resource usage, prolong product life, and enable efficient recycling or disposal, minimizing waste and environmental impact.
Example: Using PLM, a company establishes a product take-back program, ensuring proper recycling and disposal of products at the end of their life, reducing landfill waste and associated emissions.
How Lean and Green Manufacturing compliment PLM?
Lean and Green Manufacturing (LGM) complements PLM by focusing on waste reduction, process optimization, and sustainable practices. LGM principles align with decarbonization objectives, as they aim to minimize resource consumption, reduce emissions, and enhance overall operational efficiency. By integrating LGM methodologies with PLM systems, manufacturers can identify areas of waste and inefficiency, implement lean processes, and adopt sustainable practices throughout the product lifecycle. LGM brings a holistic approach to decarbonization by optimizing production workflows, reducing energy consumption, and promoting a circular economy mindset. The combination of PLM and LGM creates a powerful synergy, facilitating the transition towards a more sustainable and low-carbon manufacturing industry.
Conclusion:
In the journey towards decarbonizing the manufacturing sector, PLM plays a vital role by integrating sustainability into product development, optimizing energy usage, facilitating supply chain collaboration, and enabling efficient lifecycle management. By embracing PLM within the framework of Industry 5.0, manufacturers can achieve sustainable growth while reducing their environmental footprint.
Buy Industry 5.0 book from here.