“Preparation is the key to success” — Alexander Gramham Bell, inventor. Here is the comprehensive breakdown of production planning for manufacturers looking to optimize their production sequencing.
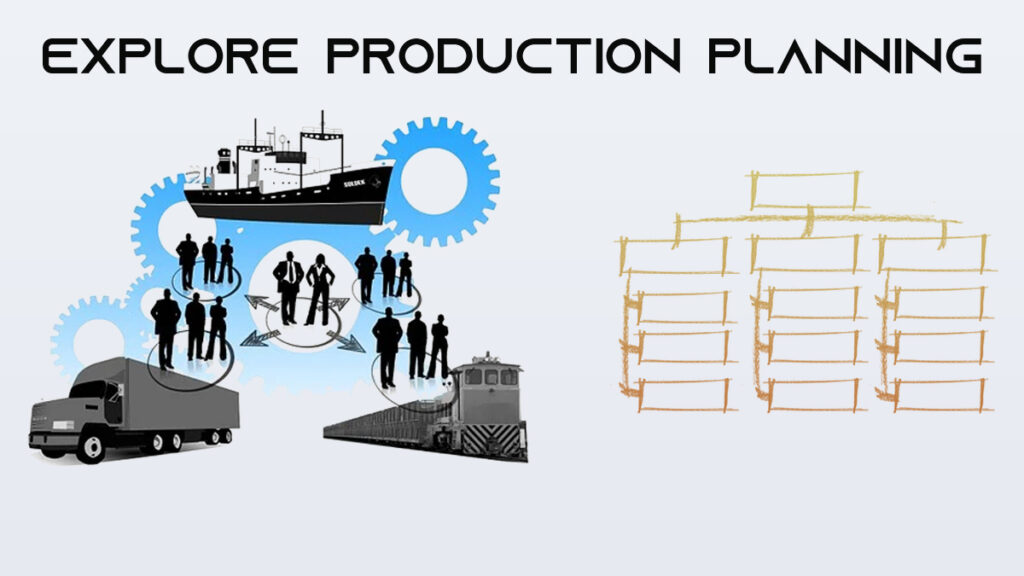
Having no plan leaves you unprepared — like going into a mineshaft without a flashlight.
How are you supposed to see where you are going if you’re completely in the dark? Maybe you feel like taking a moment to theorize production is a waste of time that could be better spent producing products. But, without a plan, you’re going to constantly run into low stock levels, delays, high manufacturing costs, and dissatisfied customers.
That’s why we’ve put together this guide to production planning to help you understand what it is and put together your own kickass plan.
What is production planning?
The definition of production planning is as follows — a set of processes manufacturers need to follow to design and produce a product or provide a service to their customers.
To expand upon the production planning definition, you can think of it as a roadmap or strategy that you’ve developed based on the requirement planning of your business before you commit anything to production. These requirements will consider factors like managing your supplies chain, raw materials, resources, factories, and warehouses. Depending on a business’s size and scale of manufacturing, a production manager is responsible for developing a production plan by working closely with shop floor workers, contractors, and different departments within the business.
So, what is the primary task of production planning? Well, there are three that a manufacturer needs to achieve for flawless production planning:
- Complete efficiency when using materials, utilities, and resources
- Reduce manufacturing waste and eliminate excess materials in the purchase management process
- Efficiency utilizing workforce management, the amount of production times required for making goods, and equipment availability
As you can already imagine, your production plan will heavily depend on your manufacturing setup.
However, most manufacturers follow one of two types of planning – make to order or make to stock businesses:
Make to order – You create manufacturing orders after receiving a customer order. Your production plan will need to anticipate customer orders.
Make to stock – You create manufacturing orders based on demand. Your production plan needs to produce a certain inventory level within a specific time period.
What are the main differences between production planning and scheduling?
Production planning – The process of creating a plan which will detail the materials availability and resources needed to meet forecasted demand
Production scheduling – The process of determining exactly when materials, resources, and equipment will be needed
Check out katana article Production planning and scheduling for manufacturing to learn more about introducing a schedule into manufacturing.
Why is production planning important?
As already touched on in the previous chapter, your production planning is important because it affects other aspects of your business.
Developing a production plan for optimizing flow means identifying what are the most important aspects of your business, for example:
- Supply chain management
- Production scheduling
- Material requirements planning
- Manufacturing lead time
- Resource capacity planning
Production planning allows an owner or manager to create an efficient production process to meet customer and organizational needs.
A great production plan will empower manufacturers to get total control over their production processes. It does this by providing knowledge on what and how long is needed to finish a production run. This then allows manufacturers to:
- Better manage their time
- Avoid bottlenecks
- Manage staff
- Create a seamless process flow in manufacturing
Without a proper production plan in place, it’s easy to lose control of your resources and manufacturing — leading to delays, shortages, and increased product costs.
5 types of production planning
Make to order and make to stock are workflows that will impact how you develop your production plan. Your plan will also be affected by your manufacturing processes too. Here are the five main methods of production you can introduce into your business:
1. Job method
The job method, or job shop manufacturing, is often used when manufacturing a single product where custom material processing requirements are needed. For bespoke manufacturing or any production where customization is offered means your production plan will change from product to product. SMB manufacturers usually implement this method, but larger companies can utilize it too.
2. Batch production method
The batch production method, or batch manufacturing, produces finished goods in bulk instead of individually or through continuous production. This production process allows manufacturers or managers to closely watch each stage of production to make quick corrections and monitor efficiency. This method is great for food production or any manufacturers who produce a large scale of items.
3. Flow method
The flow method, or discrete manufacturing, is a demand-based manufacturing plan where materials ‘flow’ from one machine to the next until they become finished goods with little human interaction. This approach to manufacturing requires a standardized workflow and increased quality control to ensure the continuously produced items aren’t defective. This method is great for manufacturers who need to produce a uniform set of items one by one.
4. Process method
Process method, or repetitive manufacturing, is the stereotypical idea people have of manufacturing – your assembly lines. This production plan will create finished goods by passing through different machines and processes. Great for manufacturers who need to make a lot of similar products.
5. Mass production method
The mass production method, or continuous manufacturing, is more or less the same approach as the flow method, but on an even larger scale. Manufacturers use this method if uniformity is critical, and they use a standardized process to guarantee that products all look the same. Using the mass production method allows manufacturers to produce many products in a short amount of time.
5 production planning processes to help you develop your plan
To put together your production plan, you’re going to need to follow these five processes:
1. Forecast your demand
Forecasting demands, or demand planning, is the investigation of future customer demand, based on several factors such as:
- Historical sales data, collected from Gantt charts for example
- Local and national taxes and regulations
- Current trends and future predictions of consumers
- Technological advancements
Learning and understanding your product demand will help you make the best choices when arranging and improving your operations.
If done properly, you can estimate what resources you’ll need and how much raw materials will be consumed during a production run. You can put together a solid prediction of future sales — but it doesn’t mean it’ll be accurate — it’ll just give you an idea of what to prepare for. Demand planning is continuous as anything can happen internally or externally that will affect sales.
2. Inventory control
Mastering inventory control is critical for scaling your business and shouldn’t be overlooked.
Inventory control concerns itself with understanding where all inventory is and ensuring that it gets to where it needs to be. This isn’t to be confused with inventory management, as that includes processes like inventory costing, buying policies, and selling price. If you establish proper inventory control, you can keep the right amount of products flowing through your business uninterrupted.
3. Resource management
Understanding how to manage resources in a manufacturing setting is important because not only are you managing people, you’re managing machines, tools, workspaces, contractors, materials, and anything else your production might require.
A quick and easy way of managing your resources is by developing a capacity plan. This will allow you to understand the maximum capacity of your manufacturing and if it’s enough to help you produce the number of products you need. Without a capacity plan, it’s impossible to develop a production plan.
4. Monitor production
The first three points will be enough to help you put together a decent production plan – but now you need to monitor your operations to see if your production plan is actually working.
Document your production run and compare the results to your production plan. Doing this will help you identify bottlenecks in your business. Then, you can address these issues, redevelop your production plan, and monitor the process again.
5. Master production schedules
Once your production plan looks achievable, you can progress to the next step, producing a master production schedule, the ultimate document for production.
Your master production schedule (MPS) will detail how many items need to be produced within a certain period. Once you’ve determined your capacity, demand, and production plan, all of this information will be used to create an MPS document. Most manufacturers use manufacturing technology to create an MPS that will provide real-time data and allow manufacturers to make production changes on the fly.
A simple production plan in action
Let’s imagine a small but modest workshop with five artisans making psychedelic t-shirts.
Each of the artisans works eight hours a day, from Monday to Friday. They follow a make-to-stock workflow in a job shop setting. To produce one t-shirt takes two hours.
The max capacity of this Funkadelic business is 200 hours.
In this scenario, the annual hippie fest is fast approaching — and looking at your historical data collection — the t-shirt makers are expected to see a surge in sales. Last year they were overwhelmed, so this year they have decided to put together a quick production plan, a week in advance of when they’re expecting an increase in demand. They also want to have a safety stock level of ten for each of their items.
Their very simple plan looks like this:
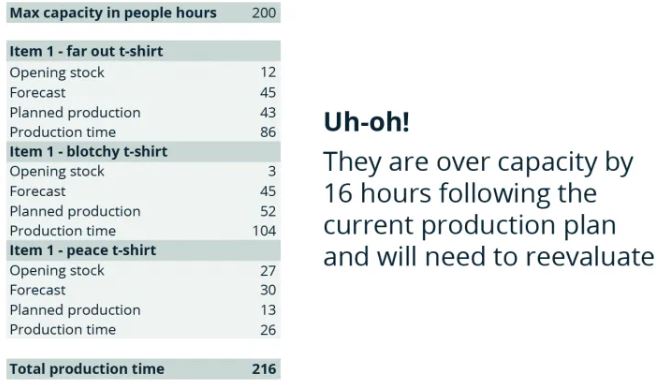
As you can see, their current plan means that they won’t be able to meet production requirements, but they can now use this knowledge to readjust their current production plans to something more like this:
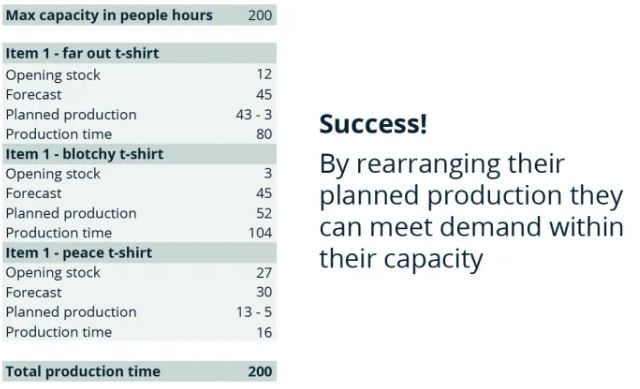
They can now meet demand by sacrificing some of their plans to store safety stock and still have some stock left over.
However, this plan put their operations and resources at 100% capacity. If one of the artisans calls in sick on Wednesday, the max capacity for the rest of the week will drop to 176 hours. When planning production, a rule of thumb is to have 20% free to give yourself wiggle room if a problem occurs.
The above — but very basic and simple — plan is only for one week. Your production plan will need to cover several weeks.
KPIs to track your production planning
Now you know everything there is to know about putting together your production plan — the next step is understanding how to measure its effectiveness.
Here are some KPIs to track to get you started:
- Manufacturing costs — track how much it costs to produce an item by looking into raw materials, utilities, salaries, rent, etc.
- Capacity utilization rate — you don’t want resources running at max capacity, but you don’t want machinery or workstations sitting idle
- Planned production vs. actual hours — this will help you better understand how long it takes to produce an item or uncover any issues which lead to delays on your shop floor
- Employee utilization (productivity) — is the same as your capacity rate. The only difference is that you don’t want to overwork them. If an employee scheduling means they have an 8-hour workday, it doesn’t mean you have to push them to do 8 hours of work. This can lead to burnout
- Takt time — a lean manufacturing concept that looks into the actual time it takes to produce a single unit of item
Using this checklist will guide you to create your business analytics to observe your production and develop plans to make them even more efficient.
But, as you can tell, doing this is a long and arduous process, and many scaling manufacturers turn to automation to help them with this task.
Ditch the spreadsheets for Katana ERP manufacturing software
Katana ERP manufacturing software gives 1000s of manufacturers the tools to develop production planning and scheduling (APS — Advanced Planning and Scheduling) automatically.
It does this by taking your needed materials, resources, and staff and automatically allocating materials to production, as well as calculating estimated deadlines and manufacturing costs. The nifty drag-and-drop system means you or your managers can reprioritize manufacturing orders, and Katana will intuitively redesign your production plan. Best of all, Katana is a cloud-based software, meaning as long as you have an internet connection, you can access important business information from anywhere.
Taking what would usually be a lengthy day-long process and giving you a production plan in a matter of minutes at a click of a button.
Easily reduce inventories inconsistencies with an ERP system.
Need help putting together your production plan? Sign up for Katana’s 14-day free trial and see firsthand how easy it is to create a dynamic production plan.