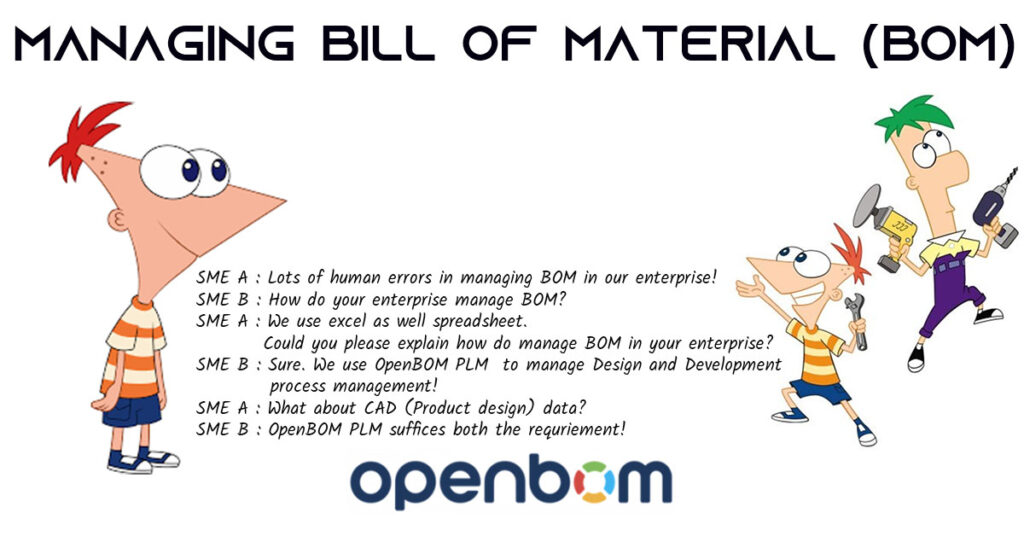
Bill of materials (BOM) or Bill of products (BOP) is the primary function of any type of manufacturing process in across different manufacturing sectors. BOM, is the detailed checklist of all required parts, items, resources, and assemblies that a manufacturer needs to make a final end product. It is very important to develop BOM prior to starting to produce an item. BOM go through several iteration before transforming to a completed product, which suggests it’s also likely to be handled by several team members of the product design and development team. Making use of excel or spreadsheet to manage a BOM is a traditional circumstance for most of the small to medium production enterprises. Yet managing BOM in excel or various other means not optimal, as information needs to be continuously returned to opening expensive human mistakes that can shake off entire product design to manufacturing, besides it is challenging to track what variation of the record is being shared as well utilized by the NPD/NPI personnel.
So, what is BOM and its types?
A BOM is a considerable list of resources, elements and also settings up called for to construct, repair an item or manufacture a product. A BOP usually appears in a hierarchical style, with the highest level showing the finished item and the bottom level showing specific components and also materials. There are different kinds of costs of products particular to engineering utilized in the design procedure, and certain to producing utilized in the constructing procedure.
While there are several sorts of BOM’s, a few of which are distinct to specific business markets, two types attract attention as the most typical- engineering and manufacturing BOM.
Engineering Bill of Material (eBOM)
The eBOM is established throughout the item layout phase and is commonly based upon Computer-Aided Design (CAD) or Electronic Design Automation (EDA) tools. The file usually details the things, parts, parts, subassemblies as well assemblies in the product as developed by the design group, frequently according to their relationships with the parent and child item as stood for in its assembly drawings. And it’s not uncommon for greater than one eBOM to be associated with one completed product.
Manufacturing Bill of Materials (mBOM)
When a service requires to reveal all the settings up and also parts needed to build a completed product, the mBOM is utilized. Components that need handling before assembly have to also be consisted of in the mBOM. The paper contains details that is shared to all the integrated company systems included in purchasing parts and also building the item, consisting of enterprise resource planning (ERP), materials resource planning (MRP) and also, in some situations, manufacturing execution system (MES). This is one of the most typical sorts of BOM for a manufacturing company. The mBOM depends on the precision of the quantities of components purchased throughout the manufacturing process. This helps make certain that the investing in division can maintain the optimum timetable for ordering the required components and also discuss the very best possible rate from relevant vendors.
Service BOM
The Solution BOM (commonly developed by engineers throughout the design phase) commonly includes a list of all the parts, setup steps and repair work guidelines that service technicians make use of when servicing a product or mounting onsite at the customer’s business.
Sales BOM
Unlike other kinds of BOMs, a Sales BOM gives details of a completed item before its assembly during the sales stage. In a Sales BOM, both the end product and also the components look like different products in the sales order record. In enhancement, the parent product will be listed only as a sales product, not as a stock product as well as the kids will be detailed as subitems.
Configurable BOM (cBOM)
A cBOM includes all the components needed to produce and also make product to a customer’s particular needs. The cBOM is commonly made use of in sectors that have extremely configurable items such as work stores, heavy equipment and commercial machinery.
Challenges faced:
Difficulties in maintaining and managing BOM for manufacturing enterprises because of various variables like item intricacy, design adjustments, communication, along with service procedure circulation. Determining what information to capture, who can make changes, and how to track these changes are essential elements to think about when developing a BOM, and also spending the time to make a BOM monitoring process will produce the highest degree of clearness and the most effective interaction (amongst staff member, throughout divisions, suppliers and contract manufacturers), change control, version control and business process automation.
BOM Management with OpenBOM PLM:
Understanding of OpenBOM PLM systems, will help to enhance the NPD/NPI process with in the enterprise. OpenBOM is a SaaS cloud-based product lifecycle management (PLM) digital network platform that manages product data and connects manufacturers and supply chain networks. OpenBOM manages Parts (Items), Item Masters (Catalogs), Bill of Materials, Vendors, Planning, and Purchase Orders. OpenBOM connects the various silos of data in your organization (CAD, Bills of Material, POs, ERP/PLM, and more) in a single manageable connected process.
Final Thoughts:
Reliable product design data (BOM) management demand to develop a fail-proof system that makes certain that the most up to date version is constantly in operation by cross functional team members of NPD/NPI across the extended enterprise accessing product and also its details. For SME manufacturers collaborating with distributed groups and also supply chain companions, working together on the most recent BOM is important to reduce production errors and also delivery hold-ups.