New digital technologies, enhancing connection, the drive for advancement, a higher concentrate on services and modifications in client demands are all aspects which wait a press towards more collaborative design and manufacturing in the age of Industry 4.0.
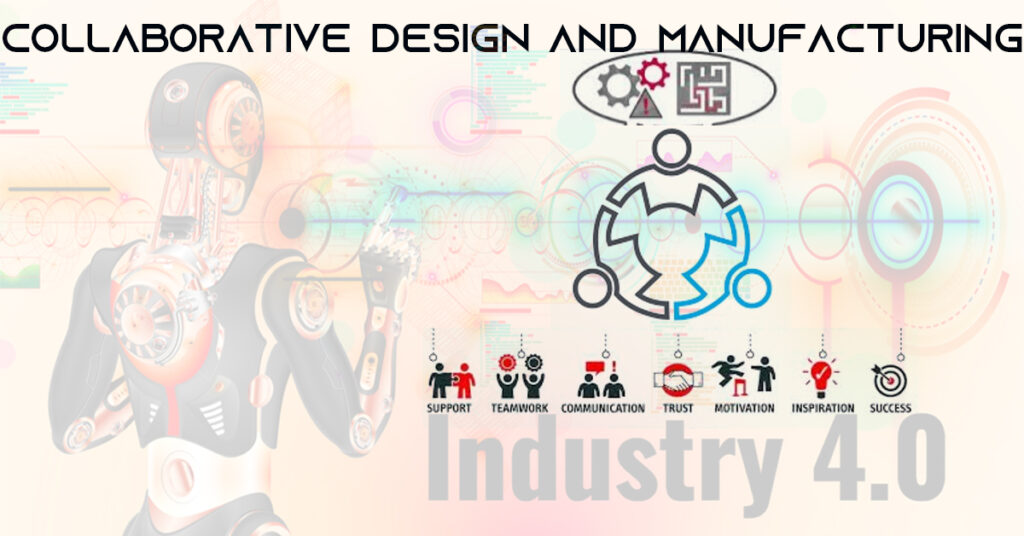
Globalization of production indicates that firms ought to be able to design anywhere, construct anywhere as well as maintain anywhere at any moment. Cooperation is critical to ongoing success in extended enterprises. Meeting worldwide demand and also replying to customer demands for tailored products is increasing the product on top of process intricacy of both advancement and also manufacturing. The demand to sustain specifying beyond managing these massive arrangement options is driving the demand for enhanced cooperation in between design engineering, process engineering, and manufacturing.
As a concept distributed collaboration is not new, and there are plenty of successful joint R&D tasks entailing colleges and also companies for many years. What has actually transformed is that cooperation has become a requirement for incumbents fighting to keep market share in the face of competition from digital disruptors. Manufacturers additionally employ collective tools throughout planning to help boost production procedures, plant layouts and tooling, and also to permit earlier impact on product layouts. Distributed collaboration can be made use of for examining designs and change orders with the design team, interfacing with tooling developers, confirming tooling setting up and also procedure; reviewing manufacturing procedure plans and factory layouts, reviewing production troubles with vendors and also coordinating tooling amongst distributed manufacturing plants.
PLM enables collaboration in product design, ERP enables collaboration in resource planning, and IIoT enables end to end collaboration in product design, development and manufacturing. With careful preparation and effort, most of these obstacles are minimized, and also advantages can be achieved. Cyber physical systems are enablers for altering business reasoning and value chains, with the conjunction of cyber physical systems and the development of brand-new service versions helping with the creation of turbulent innovations.
A brand-new kind of dispersed production system is born with the recent progression in additive manufacturing. Manufacturers have to have the ability to efficiently plan their manufacturing over and above supply method for a lean product manufacturing and afterwards have the ability to transfer that information besides customize to other distributed manufacturing plants.
Final Thoughts:
Manufacturers require to have a constant application of setup and deviation across design, planning and execution to allow expertise re-use and also develop a usual collection of ideal methods to sustain standardization.
To know more reach us at @neelsmartec.com. Glad to aid you!